Written by Clark Vargas
The significant source of particulate lead in an indoor range is the ammunition used. There are four ways lead is generated in the shooting range.
The first and worst, also because of particle size, is the primer that starts the powder ignition. It contains the chemical lead styphnate and other heavy metals that insure a proper and reliable ignition.
The second, and second worst, because of particle size, is the lead burn of the lead bullet tail of jacketed ammunition. The hot propelling gases result in atomization of molecular lead possibly the most dangerous because of great gas volumes if in haled because of range eddy currents.
The third is the lead particles spiting out of revolvers and barrel friction on all firearms. It results in varying size lead particles downrange of the firing line on the floor. The lead will be picked up by shoes and tracked elsewhere, where they may or may not be ingested.
The fourth method, and the one that generates up to 95% of the particulate lead, is the lead bullet collision with the so commonly used, “hard” 30° to 45° incline steel traps.
It is just not prudent any longer to simply design hard steel bullet traps unless “tracer ammunition” is going to be used for machine gun training.
Just by changing the projectile to totally encapsulated copper jacketed projectiles, it produces a 97% reduction in lead particulate when compared to using solid lead bullets. The use then of both lead-free primers and totally encapsulated projectiles results in airborne lead being totally, eliminated at the firing lines and breathing zone.
Military and law enforcement are the high consumers of ammunition and will still continue to utilizes jacketed bullets with lead primers for some time to come. The many calibers of ammunition used and trained with are, the 9mm, .38, .357, .45 calibers, 5.56mm and 7.62x51mm. 12ga slugs and double ought buck. Ammunition comes from a variety of manufacturers.
Although lead-primed, jacketed ammunition is the standard, it won’t be long before reliable non-lead primers become the new standard, along with totally encapsulated lead projectiles.
Hard bullet traps are the major reason, as much as 95% of for the unintended generation, of lead in dust and waste streams in firing ranges. Most existing bullet traps terminate the bullets energy with a metal to metal hard collision generating heat, lead slatter and fragments and dust.
Softer termination schemes such as the 12° to 17° dry or wet funnel type traps with deceleration chamber and/or swirl chamber or snails are much gentler and produce no dust.
There are three antiquated metal bullet traps most common and still in use today; the escalator type, the venetian blind type and a “pit and plate” type. Each of these type backstops has advantages and disadvantages, however the net results remain the same: hard impacting lead projectiles on hard steel, causes extreme fragmentation of the lead and production of lead dust. Gene Fabian reported in 1996 that a full 20% of the lead bullet weight shot downrange on hard steel backstops do not end up as large enough lead pieces that can be recycled. A full 20% of the lead turns to small fragments, powder and molecular lead not captured in the trap. It ends up as settled dust or in the bag house. Downrange contamination becomes the major reason that hazardous conditions have resulted in firing ranges. Unless, these steel bullet traps are frequently maintained and HEPA vacuumed, lead dust accumulates to the point that it becomes stirred each time the ventilation system is used. It has been observed that human overexposure in such cases can occur even in the absence of shooting.
The major improvement over the antiquated steel traps discussed above are the soft traps of 30° and less angle plate dry or wet funnel type bullet traps. The collision is a lot softer on projectiles since bullets impact the plates at a 12 to 17 degrees or less incline and slide into a swirl or deceleration chamber. Any dust that is produced can purportedly be vacuumed by an exhaust fan and directed to a filter chamber or washed into a water oil mixture.
Two problems can occur with the dry-funnel design. The first is, the shooting range is designed as a negative pressure room that can easily overcome the bullet traps aspiration fan capacity and may result in lead dust settling in the range room anyway.
The second problem that occurs is that over the life of the trap, lead smearing will occur even with jacketed and hollow point ammunition. When the range is finally closed, all the steel will have to be disposed of as hazardous waste or cleaned.
Because of the concern for lead dust generation at steel bullet traps, the bullet trap manufacturers have made efforts to do research and develop new traps. In 1989, Ron Coburn designed a funnel trap utilizing water and oil film on the impact plates to totally eliminate the dust generation from the projectiles impact on the steel impact plates. Although very effective in reducing downrange contamination, it is believed to increase long-term maintenance cost. Cost, due to the creation and the recovery and disposal of a hazardous water oil waste, increase in humidity and clogging of the recirculating system with paper bits. That has made it difficult for designers to fully accept this method as being the answer to bullet traps. However, it has promise aesthetically. Increased (oil/water) humidity in the range, we are told by users, makes the range seem slippery and paper pieces in the water that make it a past the screens stops flow and burns out the pumps.
Probably the closest to desirable to date of the soft traps that works best are the low volume shooting chopped rubber traps. These bullet traps capture projectiles intact and allow for full recovery without generating a mixed waste stream. The bullet trap is constructed on a concrete sloped floor or preferably with a steel support frame and a soft rubber sheet front, which allows all bullets to penetrate intact 4 to 6 inches into the matrix. The space created between the steel and rubber sheet is filled with pieces of recycled rubber tire sidewalls. Bullets pierce the front rubber sheet and then the square rubber pieces stop the bullet intact through friction by about 6” deep from the surface. The bullets and the rubber pieces are periodically extracted from the bottom through a slide gate fully intact, ready for recycling. The trap must be recycled monthly to preclude the hard armorizing packing of the rubber surfaced with lead. Once every 18 months or so, the rubber must be shoveled out and a complete sifting must be done. These traps can also catch fire so a fire retardant is added to eliminate that condition. If these traps, which are labor intensive, are not maintained they wouldn’t work as intended.
Tests performed on soft rubber traps reveal that there are no lead emissions generated at the trap; furthermore, the rubber pieces do not exhibit a hazardous characteristic for lead under the RCRA TCLP definition. The rubber material can be reused for the life of the trap and not result as a hazardous waste upon closure.
The choice of bullet trap also very much affects the ventilation design and cost. Rubber traps require two (2) stage filtration and steel backstops require three (3) stage filtration. Both require HEPA filtration as the last filter.
LEO’s need to train with their carry ammunition. In my opinion, round nose totally encapsulated ammunition introduced in the 1960’s or jacketed hollow point with no lead primers fit that bill, both at economic prices. They are fully equivalent, ballistically to any of the duty ammo. That is what I recommend in my designs.
Ammunition manufacturers have taken the initiative but perhaps sometimes in the wrong direction, at the behest of the Federal Government over the last 12 years, to research lead-free bullets and lead-free primers. “Green ammunition” is the result.
“Lead free bullets”, the “Green Ammunition” are the politically correct, all encompassing terminology applied that does not offer much definitive information on how to solve the problem. Green ammunition includes zinc ammunition, frangible copper ammunition, solid copper ammunition, soft nose zinc ammunition, jacketed wound zinc ammunition and jacketed tungsten ammunition, etc. Each provides alternatives for trap and ventilation design but does not eliminate the recycle problem and each has unintended consequences. Bullets manufactured out of non-lead ingredients appear to pose less of a risk to humans, when the ammunition also incorporates lead free primers, but pose equal or greater risk to the environment than the lead munitions.
None of the metals used for “green ammunition”, when out of place, are environmentally benign. For example sintered copper bullets the one “green bullet” out of the bunch, which still seems viable turns to fine powder upon impact with the trap or steel target. The fine copper now has to be collected and recycled in its entirety or environmental problems will result. Copper acts is a fungicide and is detrimental to marine organism larvae.
When zinc projectiles are used and are shot into existing lead deposits, the value of the lead deposit goes to zero since that deposit can no longer then be recycled. It must now be disposed of as hazardous waste. We also understand that shortly wound zinc projectiles will no longer be manufactured. How many recyclable lead deposits on ranges have been ruined and are now hazardous waste, because zinc bullets were used?
(This article continues in next week’s newsletter)
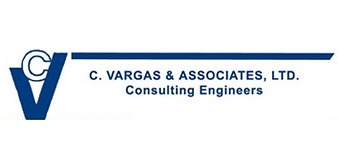
Clark Vargas is a professional engineer and President of a successful 23-year-old civil/environmental engineering firm and has designed more than 30 shooting ranges in Florida, New York, Virginia, Tennessee and Kansas. He also is President of the Florida Sport Shooting Association, the NRA’s official state association. He shoots conventional and international pistol competitively and has been invited to shoot for the U.S. Pistol Team try-outs. Mr. Vargas is Past President of the Gateway Rifle and Pistol Club, a 2,200-family member shooting club in Jacksonville, Florida, an endowment member of the NRA, and the NRA’s 1999 Achievement in Range Development Marlin R. Scarborough Award recipient.
(NOTE: Action Target has republished this article in its entirety with the permission of the author. Ideas, comments, practices, recommendations, etc. are the author’s own and do not necessarily represent those of Action Target. Our line of indoor range products, which include our steel Total Containment and rubber traps, ventilation and dust collection meet and/or exceed all of Mr. Vargas’ recommendations/conclusions.)